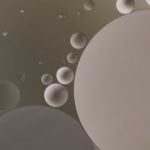
Seqens introduces mobility in its maintenance and inventory management processes
French chemical group, Seqens has chosen to equip its operators in the field with mobile solutions provided by HRC Software, in order to optimize its maintenance and inventory management processes.
Based in Écully, near Lyon, Seqens is an industrial group in the chemical sector, with a worldwide presence: 24 production sites and 3 R&D sites, spread over Europe, North America and Asia. The group supports its customers from research to industrialization of production, particularly in the pharmaceutical sector. To optimize the maintenance and inventory management processes in its plants, Seqens has chosen to implement mobility solutions provided by HRC Software. These enable it to collect data and bring useful information as close to the field as possible.
Our IT organization is positioning itself as a partner to the business community: it is called ISB, for Information Services for Business
Its objective is to provide solutions to business needs, in line with the group’s strategic roadmap. Seqens is growing rapidly and has embarked on a strategy of digital transformation of its plants in order to optimize its production. Within this framework, the group is pursuing three priorities: guaranteeing the safety of its employees, implementing continuous quality improvement and finally increasing its industrial productivity. “All of our research for solutions is oriented towards one or more of these areas,” emphasizes the CIO. To this end, IT has gone out to meet with operators to understand the problems they face, in order to respond in a relevant way while taking into account the constraints specific to the group’s activities.
As a chemical company, we have to implement appropriate protective measures, in accordance with ATEX regulations. We also have to comply with our customers’ regulatory standards, particularly those of the pharmaceutical industry, such as the GmP standard
CMMS and spare parts management
Thanks to the needs collected from operational teams, IT has identified a first use case around mobility, applied to the maintenance processes of an industrial site.
One of the challenges was to provide real-time information from our SAP ERP system to operators, for example, to indicate that equipment is under maintenance so that they don’t go nearby. We also wanted them to be able to give a feedback from the field, for example by taking a picture of a broken equipment, in order to open a maintenance ticket as quickly as possible
So, this project met both the group’s safety and productivity requirements, by helping to improve the equipment availability rate. A second case of use involving mobility, quite similar in terms of technical requirements, has appeared in another plant. This time the aim was to facilitate the management of spare parts at a site with five stores, with more than 23,000 items of equipment to manage and 10,000 items in stock.
The employees needed to improve their visibility on stocks. Until now, they had had to use a PC in an office to enter incoming and outgoing stock into the ERP system,” says the CIO. “We wanted to digitize this process completely, so that the warehouse managers could perform these operations directly on site, simply by scanning barcodes.
To meet these two needs, it was necessary to equip operators with suitable mobile terminals on the one hand, and to provide them with the necessary mobile applications on the other. The choice of terminals had to meet several criteria: they had to be large enough to provide comfortable on-screen reading, while still being easy to handle by people wearing protective gloves. The terminals also had to be resistant to falls, with a hardened shell, and not emit ionizing radiation in order to comply with ATEX standards. Finally, they had to be able to easily connect to different networks, but also to be able to operate in disconnected mode. “We opted for Ascom and Zebra terminals,” says Gultzgoff.
Industrializing mobility
At the application level, Seqens chose to work with HRC Software, both for the knowledge the company had of the chemical industry and for its very model. “Thanks to their position as a software publisher, we can have off-the-shelf solutions, which is important when you need to move fast,” says Alexandre Gultzgoff. However, in the first case of use, the needs were quite specific. Around the HRC Software platform, Seqens therefore co-developed a mobile application adapted with the publisher, a work that was spread over a little less than a year. On the other hand, in the second case, HRC Software had a ready-to-use application, which the manufacturer was able to deploy in a few weeks, the time it took to configure and train the employees. Both applications, whose interface is based on SAP Fiori, connect to the ERP via the Neptune Software platform.
Today, both use cases are in production at the two sites concerned, and more sites are planned.
We don’t impose solutions, it’s the most advanced sites on a subject that show the benefits to others, and the deployments are on a voluntary basis
The group also plans to extend the HRC Software platform to connect it to another ERP system within the group. For Alexandre Gultzgoff, one of the lessons learned from the first deployments is not to underestimate the effort involved. “It’s difficult when you start a project like this to grasp all the implications of industrializing mobility: you have to choose the right terminals, make sure that the network is present on the sites concerned, plan for offline mode, or even think about enrolling the devices in our mobile fleet manager, for security and deployment aspects,” he explains. “These projects are much more complex than we think, and they involve all the IT teams: digital Workplace, infrastructures, ERP… This breaks down the silos, including within the IT department,” he observes.
Article written by Aurélie Chandeze, Associate Editor for CIO
Follow the author on Linked In